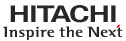
TOKYO, Nov 27, 2019 - (JCN Newswire) - Hitachi, Ltd. (TSE:6501) has announced that Hitachi developed a new automation technology of 3D culture(2), solving problems of the previous 3D culture using Hitachi's Automated Cell Culture Equipment for iPS cells(3). Automation of both 2D culture(4) and 3D culture using this equipment makes it possible to automatic massive manufacture a variety of cell types such as cardiomyocytes, meeting customer needs. The automation technology was developed by collaborative research with Myoridge Co. Ltd. which has culture technology of iPS cell-derived cardiomyocytes by the protein-free method.
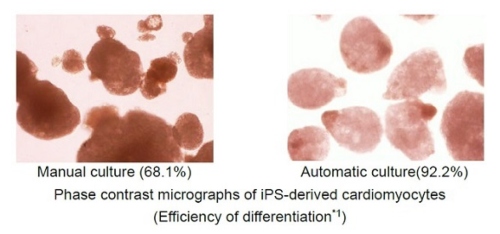
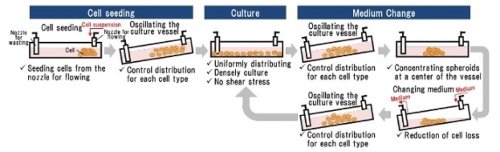
A schematic diagram of automated new 3D culture*10
Furthermore the support service to establish an automatic manufacturing process for customers who are considering automation of manufacturing regenerative medicine products will be started on December 1st, 2019. As for the service, Hitachi will examine customers' manual manufacturing process to find out the important parameters, and suggest how to optimize them by the development knowledge of automation technology of 3D culture.
Expanding the market of regenerative medicine to recover the functions of tissues and organs is expected in recent years. A large number of cells are required for regenerative medicine but it is difficult to manufacture an enough amount of cells manually. So the automation technology of mass cell culture is necessary to expand the market of regenerative medicine.
Hitachi had been developing automation technology of mass iPS cell culture, and developed the automated cell culture equipment for iPS cells for research use in June 2017. Adopting the closed flow channel for the connection of the culture vessels and the medium bottles, the equipment is capable of cell seeding, culturing, and monitoring in sterile environment and offers stable supply of high-quality mass cells. Hitachi commercialized the automated cell mass culture equipment which has the necessary functions to comply with the Japanese regulation, GCTP(5) for the first time in Japan(6) in March 2019.(7)
Hitachi automated the new 3D culture (low medium cost, low shear stress(8), and simple medium change process) by collaborating with Myoridge, solving problems of the previous 3D culture. The previous 3D culture has problems such as using a large amount of medium because of the height of the culture reactor, the shear stress to cells from the agitating medium, and the complex process of medium change. Hitachi started the collaborative research with Myoridge in October 2018 and developed the automation technology of the new 3D culture by distributing spheroids both uniformly and densely on the cell culture vessel for 2D culture. Furthermore, Hitachi manufactured cardiomyocytes by the automation technology more effectively than by manual. The technology is probably able to be applied to a variety of cell types and make them be manufactured automatically.
Hitachi also will start the support service to establish an automatic manufacturing process using automated cell culture equipment for iPS cells for customers who are considering automation of manufacturing regenerative medicine products by 2D or 3D culture. Each manufacturing process is different according to cell type. So automation of manufacturing requires to optimize the parameters of the equipment such as the pumping speed of cell suspension(9) and the oscillating angle of culture vessels. As for the service, Hitachi will examine customers' manual manufacturing process to find out the important parameters, and suggest how to optimize them. Hitachi will be able to support the automation of customers' manufacturing process by starting the service.
Hitachi group will contribute to expand the market of regenerative medicine by offering comprehensive solution including automated cell culture equipment, support service to establish an automatic manufacturing process, cell manufacturing facility, related equipment, and contract development and manufacturing services.
(1) Efficiency of differentiation: the rate of differentiated cells from iPS cells to cardiomyocytes
(2) 3D culture is a culture which makes cells to proliferate in all three dimensions forming aggregations.
3D culture promote differentiation to cardiomyocytes, liver cells, and so on, because the environment for 3D culture is similar to in vivo.
(3) Automated Cell Culture Equipment for iPS cells is not a medical device specified by the Pharmaceutical and Medical Device Act (PMD Act) in Japan.
(4) 2D culture is a culture which makes cells to proliferate on the bottoms of culture vessel forming single layer.
(5) GCTP (Good Gene, Cellular, and Tissue-based Products Manufacturing Practice): ordinance on standers for manufacturing control and quality control of regenerative medicine products
(6) Investigated by Hitachi
(7) Hitachi launches Automated Cell Mass Culture Equipment for iPS cells to spread Regenerative Medicine (March 11th, 2019)
(8) Shear stress: stress to cells from wave by agitation
(9) Cell suspension: a mixture of cells and liquid medium
(10) Patent pending in Japan (As of November 26, 2019)
About Hitachi, Ltd.
Hitachi, Ltd. (TSE: 6501), headquartered in Tokyo, Japan, delivers innovations that answer society's challenges, combining its operational technology, information technology, and products/systems. The company's consolidated revenues for fiscal 2017 (ended March 31, 2018) totaled 9,368.6 billion yen ($88.4 billion). The Hitachi Group is an innovation partner for the IoT era, and it has approximately 307,000 employees worldwide. Through collaborative creation with customers, Hitachi is deploying Social Innovation Business using digital technologies in a broad range of sectors, including Power/Energy, Industry/Distribution/Water, Urban Development, and Finance/Social Infrastructure/Healthcare. For more information on Hitachi, please visit the company's website at http://www.hitachi.com.
Contact:
Hitachi Ltd Corporate Communications Tel: +81-3-3258-1111
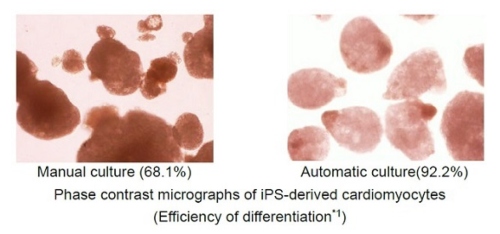
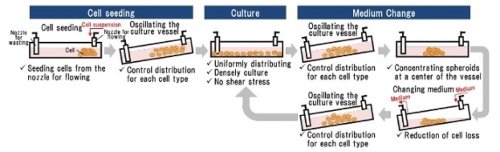
A schematic diagram of automated new 3D culture*10
Copyright 2019 JCN Newswire. All rights reserved. www.jcnnewswire.com